In https://hastings-alstrup.mdwrite.net/powering-innovation-the-future-of-hysteresis-brakes-dynamometers-and-motor-testing-systems-1744598960 -evolving world of industrial engineering and motor development, precision isn’t just a goal—it’s a necessity. Behind every high-performance motor, electric vehicle, aerospace innovation, or renewable energy system lies a suite of testing technologies that ensure reliability, efficiency, and safety. Among these, hysteresis brakes, hysteresis dynamometers, hysteresis clutches, and advanced motor test systems stand as the backbone of modern motor validation. Let’s explore how these technologies are shaping industries and why they matter more than ever.
THE HEART OF MODERN TESTING: HYSTERESIS BRAKES ⚙️
Hysteresis brakes are the silent workhorses of torque control and load simulation. Unlike traditional mechanical brakes, hysteresis brakes operate without physical contact, using magnetic fields to generate precise resistance. This frictionless design eliminates wear and tear, ensuring consistent performance over thousands of cycles.
Applications:
- Electric vehicle drivetrain testing
- Aerospace component validation
- Medical device motor calibration
- Robotics torque simulation
Why engineers love them:
1. Zero maintenance: No brushes or mechanical parts to replace.
2. Smooth torque control: Adjust resistance on the fly with unparalleled accuracy.
3. Silent operation: Perfect for noise-sensitive environments like labs or hospitals.
A recent case study from a leading EV manufacturer revealed that switching to hysteresis brakes reduced testing downtime by 40% and improved torque measurement accuracy by 15%.
DYNAMOMETERS: WHERE POWER MEETS DATA 📊
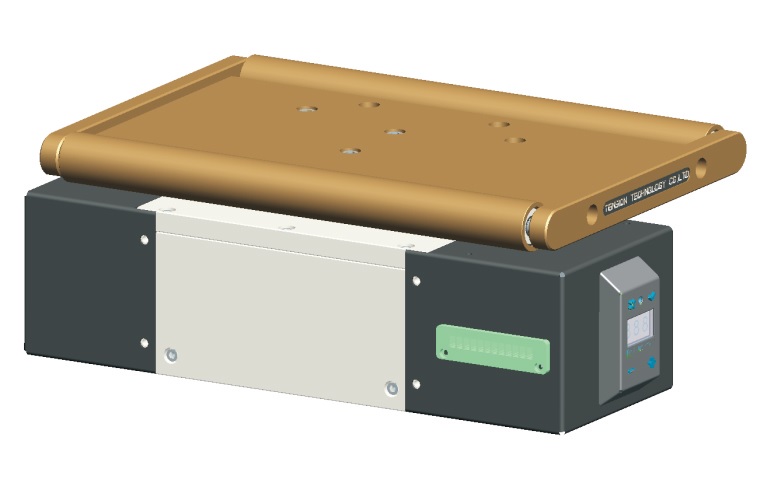
Hysteresis dynamometers take testing to the next level by combining load simulation with real-time data acquisition. These systems measure torque, speed, and power output while simulating real-world operating conditions—from extreme temperatures to variable loads.
Key features:
- Bidirectional testing capabilities (motoring and absorbing modes)
- Integration with AI-driven analytics platforms
- Customizable inertia simulation for automotive applications

Take the example of a wind turbine manufacturer that used hysteresis dynamometers to simulate 20 years of operational stress in just 8 weeks. The result? A 30% improvement in gearbox lifespan through targeted design adjustments.
MOTOR TEST SYSTEMS: THE COMPLETE ECOSYSTEM 🌐
Modern motor test equipment isn’t just about individual components—it’s about creating intelligent, interconnected systems. A state-of-the-art motor test system might include:
- Hysteresis clutches for precise torque coupling
- Multi-axis dynamometers
- Thermal imaging cameras
- Energy recovery units (recycling up to 90% of test power)
These systems now incorporate machine learning algorithms that can predict motor failures before they occur. One aerospace client reported detecting bearing wear patterns six months before scheduled maintenance, preventing a potential $2M loss from in-flight system failures.
BREAKING BARRIERS WITH HYSTERESIS CLUTCHES 🔄
Hysteresis clutches bring a unique advantage to transmission testing and energy transfer applications. By using Advanced cable rewinding , they enable:
- Slip-free torque transmission
- Instant response times (under 10ms)
- Precise control at ultra-low speeds (down to 0.1 RPM)
In robotics applications, this translates to smoother joint movements and improved positional accuracy. A collaborative robot (cobot) manufacturer achieved 0.02mm repeatability in assembly tasks after integrating hysteresis clutches into their test protocols.
THE SUSTAINABILITY EDGE ♻️
Modern hysteresis-based systems are answering the call for greener manufacturing:
- Regenerative power systems feed energy back into the grid
- Compact designs reduce material usage by up to 60% compared to hydraulic alternatives
- Oil-free operation eliminates contamination risks
A solar pump manufacturer recently reduced their test facility’s energy consumption by 70% by upgrading to a hysteresis dynamometer with energy recovery capabilities.
INDUSTRY 4.0 INTEGRATION 🤖
Smart hysteresis devices now come equipped with:
- IIoT (Industrial Internet of Things) connectivity
- Predictive maintenance sensors
- Digital twin compatibility
These features allow remote monitoring and control—a game-changer during the pandemic when engineers managed critical tests from home offices. One automotive supplier completed 95% of their development cycle remotely using cloud-connected test systems.
CHALLENGES Motor analysis and testing platforms 🔍
While hysteresis technology offers numerous advantages, the industry continues to push boundaries:
1. High-speed testing: New materials allow operation at 50,000+ RPM
2. Miniaturization: Smartphone-sized test units for micro-motors
3. Hybrid systems: Combining hysteresis and eddy current technologies
A recent breakthrough in graphene-coated rotors has doubled heat dissipation rates, enabling continuous operation at 300°C—critical for next-gen electric aircraft motors.
THE HUMAN FACTOR 👩🔬
Behind every advanced test system are the engineers who make miracles happen. Consider these real-world stories:
- A team in Munich used hysteresis clutches to replicate the muscle resistance of a human heart, improving LVAD (heart pump) designs
- Formula E engineers credit hysteresis dynamometers with helping achieve 99.8% energy recovery efficiency
- Wind turbine technicians now use portable hysteresis test kits for on-site maintenance diagnostics
YOUR NEXT STEP 🚀
Whether you’re developing futuristic electric vehicles, life-saving medical devices, or Mars rover components, the right test technology makes all the difference. Modern hysteresis systems offer:
- Unmatched precision in torque and speed control
- Adaptability across industries and applications
- Long-term cost savings through durability and energy efficiency
As we stand on the brink of an electric revolution in transportation, manufacturing, and energy, one truth remains constant: You can’t build tomorrow’s motors with yesterday’s test equipment.
[End of Article]
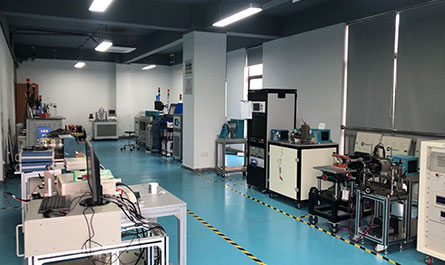